Unraveling the Secret of Porosity in Welding: Tips for Decreasing Problems and Making The Most Of Quality
In the complex globe of welding, porosity continues to be a consistent difficulty that can substantially influence the top quality and honesty of bonded joints. As we dive right into the midsts of porosity in welding, discovering the tricks to its avoidance and control will certainly be vital for experts looking for to grasp the art of premium weldments.
Comprehending Porosity in Welding
Porosity in welding, a typical issue come across by welders, describes the presence of gas pockets or gaps in the bonded product, which can jeopardize the integrity and quality of the weld. These gas pockets are typically trapped throughout the welding procedure because of different elements such as improper shielding gas, infected base materials, or incorrect welding parameters. The development of porosity can deteriorate the weld, making it susceptible to cracking and deterioration, eventually leading to architectural failures.
Recognizing the source of porosity is vital for welders to effectively prevent its incident. By recognizing the importance of preserving correct gas securing, guaranteeing the tidiness of base materials, and enhancing welding setups, welders can substantially reduce the likelihood of porosity development. In addition, making use of techniques like preheating the base material, utilizing correct welding strategies, and performing complete inspections post-welding can better assist in minimizing porosity problems. On the whole, a comprehensive understanding of porosity in welding is vital for welders to produce top quality and long lasting welds.

Typical Sources Of Porosity
When examining welding processes for potential quality issues, understanding the common reasons of porosity is crucial for keeping weld honesty and protecting against architectural failures. Porosity, defined by the existence of dental caries or gaps in the weld metal, can dramatically endanger the mechanical buildings of a bonded joint.
One more prevalent source of porosity is the existence of moisture and pollutants externally of the base metal or filler product. When welding products are not appropriately cleaned up or are exposed to high degrees of moisture, the vaporization of these impurities throughout welding can create gaps within the weld grain. Additionally, welding at inappropriate parameters, such as excessively high travel speeds or currents, can generate too much turbulence in the weld swimming pool, capturing gases and creating porosity. By addressing these typical reasons through proper gas securing, product preparation, and adherence to optimal welding criteria, welders can reduce porosity and enhance the top quality of their welds.
Techniques for Porosity Avoidance
Carrying out efficient precautionary actions is essential in minimizing the event of porosity in welding procedures. One technique for porosity avoidance is making sure proper cleansing of the base metal prior to welding. Pollutants such as oil, grease, corrosion, and paint can result in porosity, so comprehensive cleansing utilizing appropriate solvents or mechanical techniques is important.

Making use of high-grade filler products and securing gases that are appropriate for the base metal and welding procedure can substantially decrease the danger of porosity. In addition, keeping correct welding parameters, such as voltage, existing, travel rate, and gas flow price, is important for porosity prevention.
Moreover, using correct welding techniques, such as maintaining a consistent traveling rate, electrode angle, and arc size, can aid protect against porosity (What is Porosity). Adequate training of welders to ensure they follow best practices and high quality control treatments is likewise crucial in minimizing porosity defects in welding
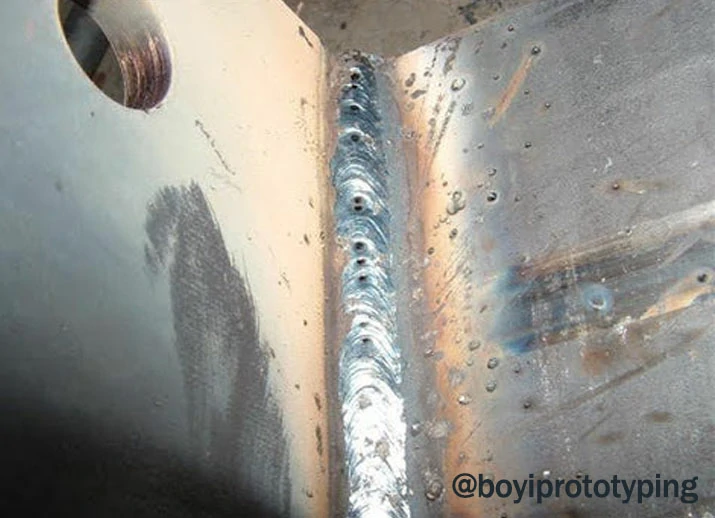
Finest Practices for High Quality Welds
Making sure adherence to market standards and proper weld joint prep work are basic elements of accomplishing regularly high-grade welds. Along with these fundamental steps, there are several ideal methods that welders can execute to further boost the quality of their welds. One key practice is keeping appropriate cleanliness More Help in the welding location. Contaminants such as oil, grease, corrosion, and paint can negatively impact the quality of the weld, bring about flaws. Thoroughly cleansing the workpiece and bordering area prior to welding can help minimize these problems.
An additional finest technique is to meticulously choose the appropriate welding specifications for the details materials being signed up with. This consists of setting the right voltage, present, travel speed, and securing gas More about the author flow rate. Appropriate criterion selection makes sure optimum weld penetration, fusion, and overall high quality. Additionally, making use of premium welding consumables, such as electrodes and filler steels, can considerably affect the last weld quality. Buying premium consumables can cause more powerful, more resilient welds with fewer flaws. By adhering to these ideal techniques, welders can constantly generate high-quality welds that meet industry standards and exceed customer expectations.
Relevance of Porosity Control
Porosity control plays a critical duty in making sure the stability and quality of welding joints. Porosity, identified by the visibility of dental caries or spaces within the weld metal, can significantly endanger the mechanical properties and architectural integrity of the weld. Too much porosity deteriorates the weld, making it extra at risk to splitting, corrosion, and general failure under functional loads.
Reliable porosity control is vital for maintaining the preferred mechanical buildings, such as strength, ductility, and durability, of the bonded joint. What is Porosity. By minimizing porosity, welders can improve the total quality and dependability of the from this source weld, making certain that it meets the performance demands of the desired application
Furthermore, porosity control is vital for accomplishing the preferred aesthetic appearance of the weld. Extreme porosity not just damages the weld but also diminishes its visual charm, which can be important in industries where appearances are essential. Proper porosity control techniques, such as using the appropriate protecting gas, managing the welding specifications, and guaranteeing appropriate cleanliness of the base materials, are necessary for producing top quality welds with very little problems.
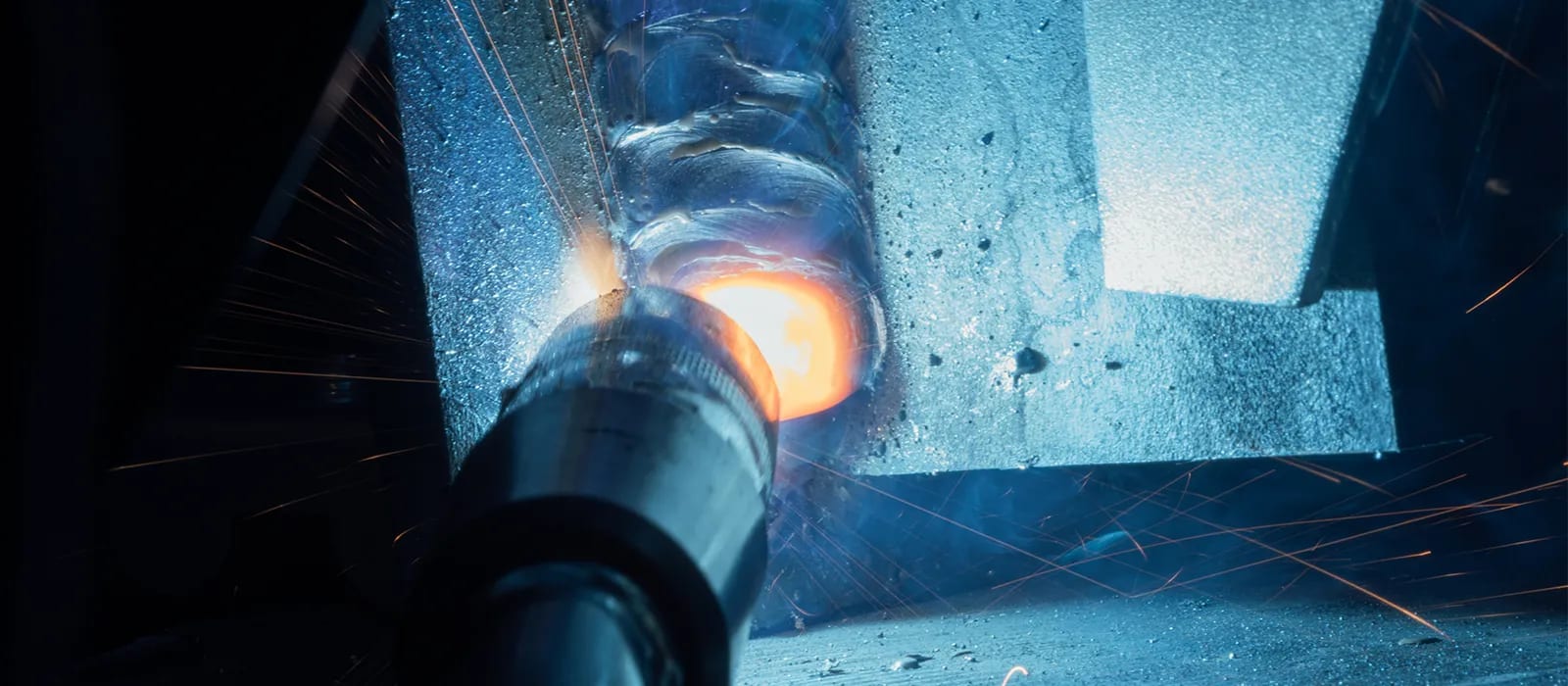
Verdict
Finally, porosity in welding is an usual flaw that can jeopardize the quality of the weld. By understanding the reasons of porosity and carrying out appropriate avoidance methods, welders can reduce defects and attain higher quality welds. It is important to regulate porosity in welding to make sure the integrity and toughness of the end product. Implementing ideal methods for porosity control is crucial for attaining ideal welding outcomes.